Successful Commissioning of a Process Line for the Transportation and Dosing of Solid Alternative Fuels to the second largest Cement Plant in Croatia
Successful Commissioning of a Process Line for the Transportation and Dosing of Solid Alternative Fuels to the second largest Cement Plant in Croatia
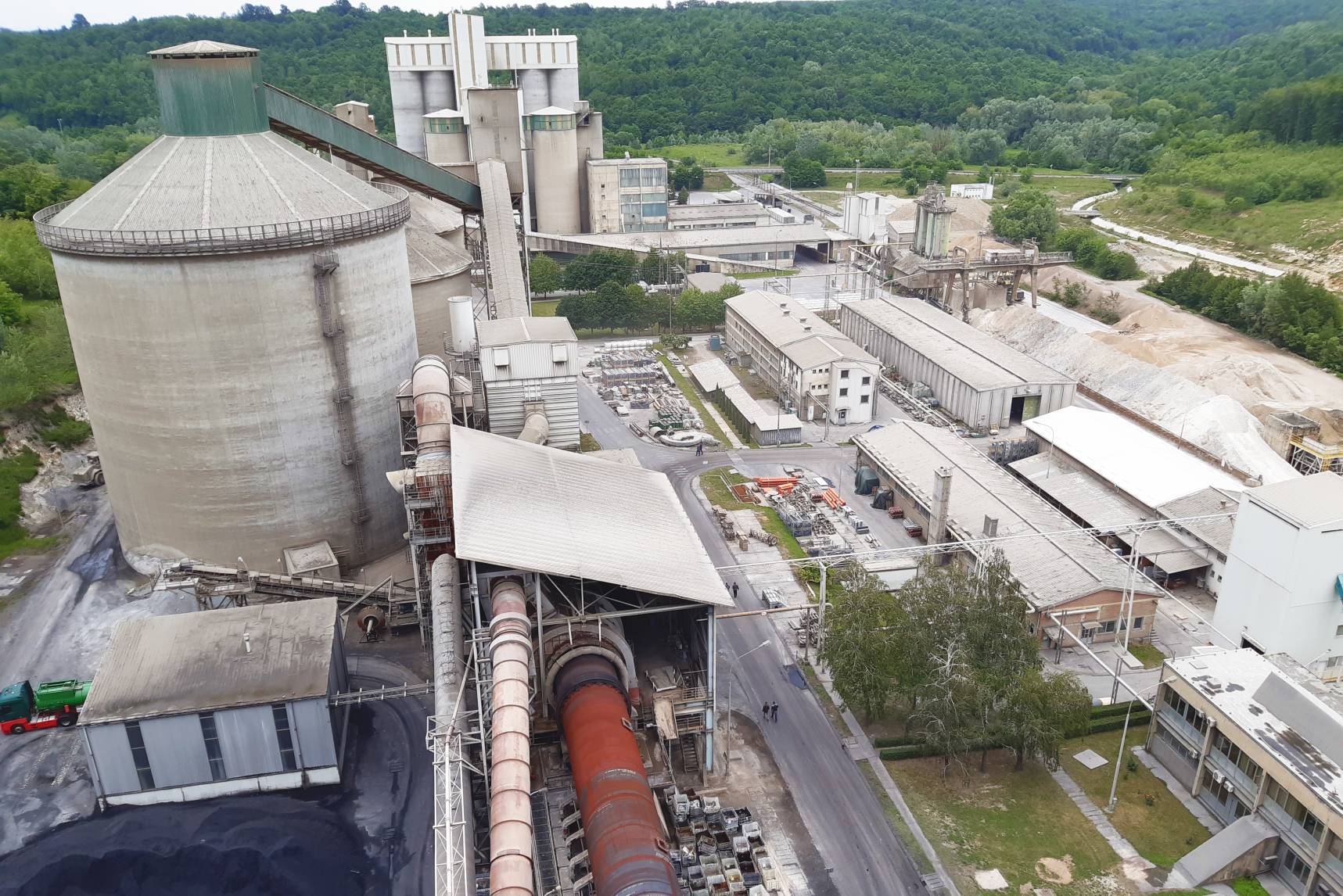
ERITECH proposed the optimal solution for the transportation and dosing of solid alternative fuels to the second largest cement plant in Croatia, Nexe d.d. in Našice which is part of the Nexe Grupa. The process line was delivered and put into operation by ERITECH within seven months
The aim of the project was to start burning solid alternative fuels in the cement plant's calciner, while it was necessary to take into account that this calciner was designed only for the combustion of primary fuels. The combustion of solid alternative fuels in the calciner was necessary, not only from the economic point of view of the operation of the cement plant, but above all from the point of view of securing the fuel base. Switching to solid alternative fuels lowers fossil fuel consumption, reduces environmental impacts and contributes to the long-term sustainable development of the economy. The project would have been a real challenge, even outside the coronavirus pandemic - the current situation, compared to the normal situation, placed extraordinary demands on high-quality project management with a high degree of flexibility and improvisation to overcome obstacles caused by the epidemiological situation.
Within seven months, it was necessary to supply the technology, including steel structures, and ensure assembly and commissioning of the technology
For the successful implementation of the project, it was necessary to coordinate all aspects of the technological parts of the design. The project started by optimally determining the position of fuel entry into the calciner channel. Since the size and construction of the calciner channel was not initially designed for the combustion of solid alternative fuels, ERITECH designed two separate inlet points for fuel injection. The injection points were located at different elevations and opposing sides. With respect to the current operating conditions and the combustion process, the positions of fuel injection have been well calculated.
Despite the limited space ERITECH managed to find a solution for the optimal dosing of material into the calciner channel.
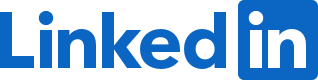